Diamond Wheels

Eagle’s Diamond Wheels
At Eagle, we’re known for top-quality diamond grinding wheels. Our synthetic diamond abrasive, known as one of the hardest materials globally, ensures maximum performance on non-ferrous workpieces. With nickel or copper coatings, our wheels offer extended lifespans for efficient and precise grinding. Whether you work with ceramics, glass, carbide, stone, composites, or more, our diverse range of superabrasive wheels will add value to your operation. Available in various shapes, our diamond wheels can guarantee burr-free cutting edges, minimal thermal damage, and reduced downtime.
EAGLE’S DIAMOND WHEEL BOND SELECTION
Our tried and true bond systems lock in the carefully selected diamond powders to ensure almost zero diamond pull out. The ingredient selection process provides a mechanical and chemical bond of the diamond particles to the bond system. This produces a long lasting, sharp and durable grinding wheel.
The Hardness of Diamond Wheels
Diamond wheels are graded by the hardness of the bond. A higher-hardness bond allows for longer wheel life when compared to conventional wheels, such as aluminum oxide and silicon carbide.
To determine the hardness of a wheel, one must first understand how the abrasive grit works.
A wheel is considered soft if the abrasive grit fractures or pulls out from the bond easily. A wheel is considered hard when the abrasive grit is held into the bond firmly, and does not result in microfracture.
Typically, if the working material is easy to cut, a high-hardness wheel is suggested. A softer wheel is used for a more difficult to grind materials, such as sub micro-grain TCT cutting tools.
The Importance of the Bond
While the diamond and coating type are an essential part of manufacturing diamond grinding wheels, the bond system selected to complement the diamond type is also a very important factor.
Our tried and true bond systems lock in the carefully selected diamond powders to ensure almost zero diamond pull out.
The careful ingredient selection process will provide a mechanical and chemical bond of the diamond particles to the bond system thus producing a long lasting, sharp and durable grinding wheel.

Eagle’s Shipping Process
At Eagle, we pride ourselves on providing exceptional solutions to your most common issues. Beyond delivering a product, we eliminate shipping issues by partnering with trusted logistics providers, guaranteeing reliable delivery, on time. Our WHEELS are engineered to your needs, optimizing performance and enhancing productivity. By investing in our solutions, many clients report extended durability and reduced maintenance costs.
Choose Eagle Superabrasives and gain a diamond wheel supplier dedicated to providing advanced customer service and expert guidance. Our team of problem solvers is ready to help you optimize PRODUCTION. Experience the difference with us and unlock the full potential of your OPERATION.
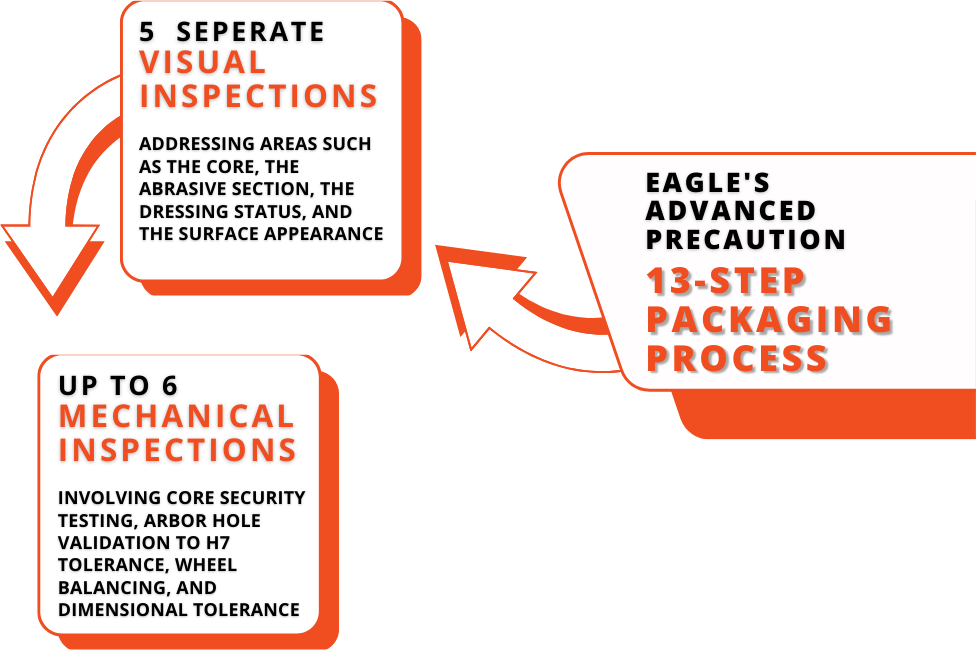

An Industry Leader
With Decades of Experience
Why Buy
From Eagle?

Trust the Experts
When you’re ready to try the best, trust the experts at Eagle Superabrasives. We offer unparalleled customer support and service.
With an extensive inventory of over 6,000 diamond, CBN and CDX wheels in stock at our North Carolina location, we are capable of shipping 90% of orders same day. Custom orders can be shipped in as little as seven days.
Our experienced staff is dedicated to providing our customers with high-quality products and excellent service. We offer technical support and advice to assist you along the way.
your grinding wheel needs.

When you’re ready, contact us for a free quote
or call us at (828) 759-5898